摩擦圧接にもデメリットがあります
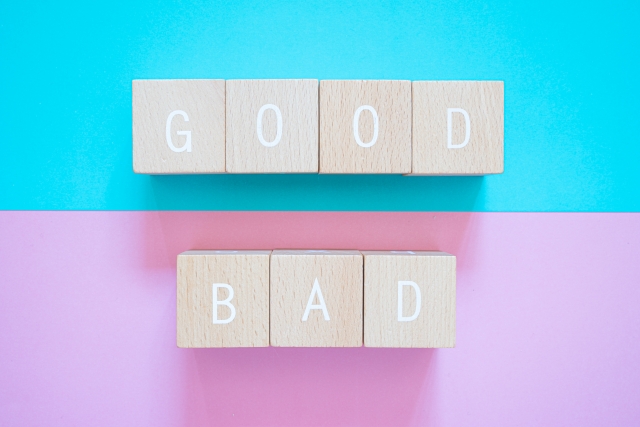
円形の断面に限る
回転させながら摩擦させるのがこの圧接技術の肝になるので、それが叶う形状をしていなければ加工することができません。 具体的には接合するのは円形の面であること、これが条件となります。 円形をしていなければ回転して押し付ける時に力が均等に加わりませんし、安定した回転をさせるには円形の断面でなければならないのです。 太い棒のような物、パイプのような物なら大丈夫ですが、角ばった物、冷蔵庫のような物は摩擦圧接では無理なのです。 材質は問題ないけれど形状がひっかかる、そんな場合も不可能と判断して他の接合方法で作業を進めることになるでしょう。 回転させ摩擦を利用するというアイデアは素晴らしいのですが、回転させた時に安定するような形状でないとこの技術は成り立たないので、そこがネックで諦めることになった部品もきっと数多くあるのでしょう。 特に複雑な形状をしたパーツは摩擦圧接が苦手とする相手です。
負荷がかかる
高速で回転させて摩擦熱を発生させるので、接合させるふたつのパーツどちらにも結構な負荷がかかり、脆いパーツだと加工の途中で破損してしまいます。 金属材料が赤くなるほどの摩擦熱を生み出す工程に耐えられるだけのパーツでなければ、回転させて圧力をかけている段階でポキリと折れてしまうかもしれないですし、 その可能性のある場合は他の方法で接合したほうが安全です。 もしも高速回転中にどこかが折れてしまったら、熱々の金属片や金属の塊が勢い良くピューッと飛んでいくことになります。 これはとても危険なことで、他のマシーンにぶつかって破壊してしまうおそれもあるので、莫大な損失が発生する覚悟がなければやれないでしょう。 またもしも人にぶつかったら大怪我をするかもしれず、火傷の治療で何時間かは作業が中断してしまうことも考えられます。 大きな金属片が衝突したのなら救急車に出動を要請する事態になるかもしれず、とにかく安全に作業を行いたいのであれば丈夫そうな部品にしか摩擦圧接は使えません。
後工程も必要
回転させて押し付けて接合するため、金属が解けたような状態で強固にひっつきますがその過程でバリが少しばかり発生します。 摩擦面に付着していた汚れなどがはじき出されるのですから、そのようなゴミを後工程で除去する必要が生まれるのです。 接合するだけでいいのならバリを取り除かなくてもいい、という発想もありますがそれではみっともない製品となりますし、美しく完成させたければバリもちゃんと除去しないとスッキリしません。 摩擦圧接されたパーツをその後どう使うのかにもよるでしょうが、そこから次の加工に進んで製品化されるというパターンが多いと思われますし、 邪魔なバリは取り除いておかないと困る、というケースの方が圧倒的に多そうです。 その手間がかかるのがこの接合方法のデメリットとなりますので、どんどん接合するだけではなくバリ取りの時間と労働力も確保しておかなければ納品の期日に間に合わなくなるかもしれません。